Carbonization furnaces play a crucial role in the production of biochar, wood charcoal, and other carbonized materials. A well-designed carbonization furnace ensures not only efficient production but also the safety of operators and the surrounding environment.
1. Temperature Control and Thermal Insulation
One of the primary safety concerns in a carbonization furnace is maintaining precise temperature control. Carbonization requires high temperatures, typically between 300-600°C, to break down biomass into charcoal or biochar. Uncontrolled temperature fluctuations can lead to overheating, equipment damage, or even fire hazards. Advanced designs incorporate:
- Automatic temperature regulation systems.
- High-quality refractory materials for thermal insulation.
- Heat distribution mechanisms to ensure uniform heating.
2. Explosion Prevention and Gas Management
The carbonization process generates combustible gases, including methane, carbon monoxide, and hydrogen. If not managed properly, these gases pose explosion risks. A well-designed furnace must include:
- A gas collection and purification system to safely extract and utilize syngas.
- Pressure relief valves to prevent pressure buildup.
- Proper ventilation systems to prevent gas accumulation inside the furnace.
Many modern biochar production equipment models, including those developed by Beston Group Co., Ltd., integrate gas recycling systems to convert excess gases into energy, making the process safer and more sustainable.
3. Fire Safety and Emergency Shutdown Systems
Due to the high-temperature environment, fire hazards must be proactively addressed. Essential safety features in carbonization furnace design include:
- Automatic fire suppression systems.
- Emergency shut-off valves to halt operations in case of abnormalities.
- Fire-resistant construction materials to prevent flame spread.
For example, a wood charcoal making machine with a sealed carbonization chamber minimizes oxygen ingress, reducing the risk of unwanted combustion.
4. Structural Integrity and Material Selection
Carbonization furnaces operate under extreme conditions, necessitating the use of durable materials resistant to high temperatures and chemical reactions. Key considerations include:
- Stainless steel or alloy construction to withstand heat and corrosion.
- Reinforced structural design to handle thermal expansion and contraction.
- Regular maintenance and inspection schedules to identify material degradation.
5. Environmental Safety and Emission Control
Carbonization furnaces can release pollutants such as particulate matter, volatile organic compounds (VOCs), and greenhouse gases. A responsible design incorporates:
- Efficient exhaust filtration systems to capture fine particles.
- Activated carbon filters or scrubbers to neutralize harmful emissions.
- Compliance with environmental regulations to ensure minimal ecological impact.
Companies like Beston Group Co., Ltd. emphasize green technology by incorporating advanced emission control mechanisms into their sawdust charcoal making machines.
6. Automation and User Safety
Modern carbonization furnaces increasingly adopt automated control systems to enhance safety and efficiency. Key automation features include:
- Remote monitoring and control to reduce operator exposure to hazards.
- Programmable safety protocols to detect anomalies and trigger corrective actions.
- User-friendly interfaces with real-time status updates and alerts.
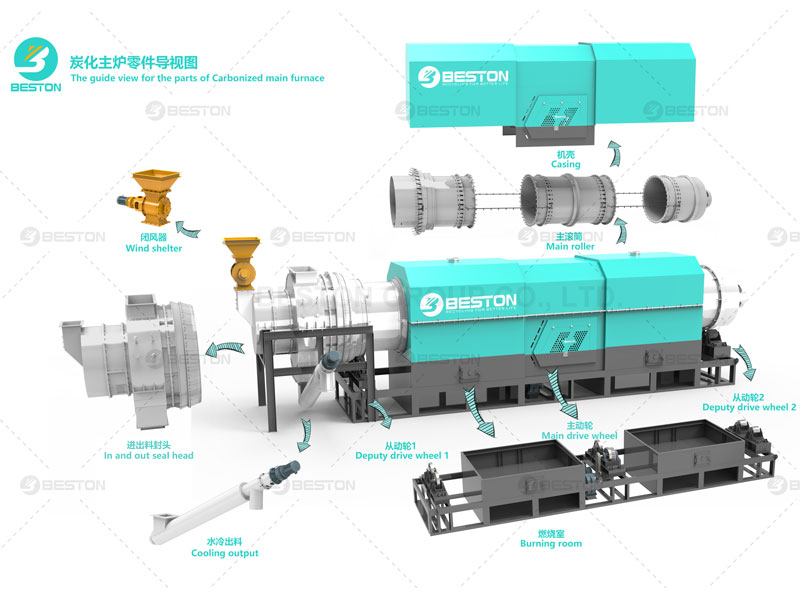
Conclusion
Designing a carbonization furnace with a strong focus on safety is essential for efficient and risk-free operation. From temperature control to gas management, fire prevention, structural integrity, emission control, and automation, every aspect must be carefully considered. Leading manufacturers like Beston Group Co., Ltd. continue to innovate in this field, integrating cutting-edge safety features into charcoal making machine. By prioritizing these safety elements, businesses can optimize productivity while ensuring environmental and operator safety.